Will Custom Implants Revolutionize Total Joint Surgery?
By: Kendal Kloiber | Contributing Editor
Published: 8/3/2023
Implants tailor-made to fit each patient’s unique anatomy may provide a better and more precise fit.
Custom implants have emerged as a valuable tool in both knee and hip revision surgery, offering potential benefits to both patients and surgeons. These implants are designed to match the patient’s unique anatomy, addressing complex cases that cannot be effectively managed with off-the-shelf components.
Custom implants are used in joint replacement surgery for patients with unique anatomical characteristics or specific defects. Previously, these implants were limited in options and relied on traditional manufacturing methods. However, advancements in technology, particularly 3D printing, have revolutionized the manufacturing process, according to Mathias Bostrom, MD, chief of the Adult Reconstruction and Joint Replacement Service at Hospital for Special Surgery in New York, N.Y.
“The ability to 3D-print with metals lets us design implants that are difficult to manufacture,” says Dr. Bostrom. “That’s been a game-changer.” With a perfect fit every time, are custom implants the future of joint repair?
Understanding custom implants
Designed using advanced imaging technology such as CT scans, patient-specific implants precisely match the individual’s joint anatomy. The use of custom implants spans the entire perioperative process, according to Dr. Bostrom.
• Initial assessment. When a patient comes to the surgeon’s office, standard X-rays and computer templates are used to determine if off-the-shelf implants would be suitable. In most cases, they are. However, if it becomes evident that they won’t be suitable for the patient, a CT scan is required to proceed.
• Imaging and consultation. After the CT scan, the surgeon and their team engage in discussions with the manufacturer’s engineers or an in-house design team. They collaborate to design the implant based on the patient’s specific needs. The surgeon further refines and tweaks the design until it is finalized.
• Manufacturing and sterilization. Once the design is approved, it is sent to the manufacturer for production. The custom implant is manufactured, sterilized and prepared for surgical use. This process typically takes several weeks.
• Implantation. On the day of the surgery, the custom implant is brought to the facility and implanted in the patient. The surgeon utilizes personalized cutting jigs, which are specific to the patient’s anatomy, to ensure precise alignment and placement of the implant.
• Rehabilitation and recovery. After implantation, patients begin their rehabilitation program, which is nearly identical to that of an off-the-shelf implant. It involves physical therapy and exercises to aid in the recovery of the joint.
Whether it’s a fully personalized implant or patient-specific cutting jigs with an off-the-shelf component, customization offers precision and efficiency advantages. Custom-cutting jigs provide more accurate alignment, require fewer trays in the OR and reduce the demand for equipment, benefiting surgery centers by facilitating quicker turnover times between procedures, says Dr. Bostrom. Not only do the custom implants improve efficiency, they also have the potential to create a perfect fit for each patient’s joint every time —though we’re far from that becoming the norm, adds Dr. Bostrom.
“Right now we use custom implants primarily for patients with very unique anatomy,” he says. “However, theoretically, each knee is a little bit different, and everyone could potentially benefit from a personalized implant that has the appropriate kinematics for that patient.”
Challenges and considerations
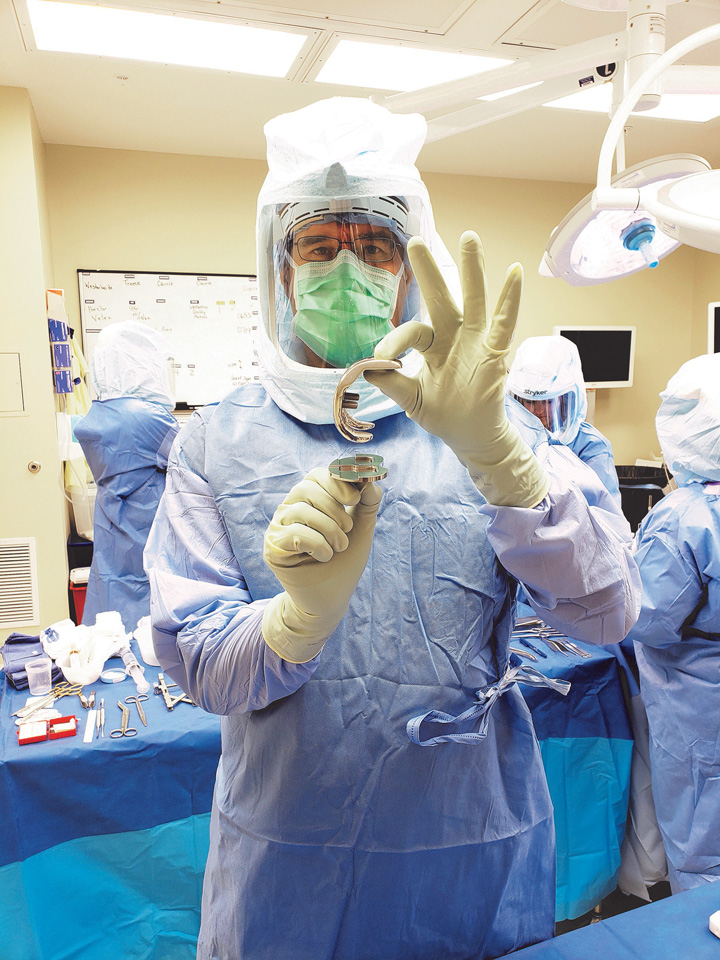
Despite obvious benefits and potential for growth, there are limitations and challenges associated with custom implants. While the manufacturing process has become faster with advancements in 3D-printing technology, it still involves a substantial amount of engineering and design time. In fact, the entire process (from designing the implant to setting it up on the 3D printer) can take anywhere from a month to three months, says Dr. Bostrom. This time frame may pose challenges for patients with acute problems who require prompt surgical intervention, especially since the off-the-shelf choices are already pretty flexible.
“Right now, we have a lot of choices when it comes to off-the-shelf options. It’s almost semi-customizable now,” says Dr. Bostrom. “We previously had two femur and one tibia size options. Now, we have 10 tibia and 12 femoral sizes, if not more, plus a variety of poly inserts.”
Advanced imaging technologies such as MRI or CT scans are another factor in creating custom implants. Facilities must ensure they have the necessary infrastructure and expertise to obtain accurate and reliable imaging data for successful implant design. And while implanting a customized joint is similar to off-the-shelf options, surgeons performing joint replacement surgeries with custom implants may require additional training to familiarize themselves with the process and technologies.
Then there’s the cost factor. The extensive engineering and design involved in creating personalized implants contribute to higher manufacturing costs. This frequently makes them more expensive compared to off-the-shelf components. The long-term performance and patient satisfaction outcomes of custom implants have also been a topic of interest, although the volume of studies on this subject remains relatively small, says Dr. Bostrom. “These are primarily being used in patients who couldn’t get anything else due to their particular cases,” he says. “So custom implants understandably are much better than suboptimal off-the-shelf components.”
Key considerations
If you’re considering the implementation of custom knee and hip implants, assess the demand for these implants among surgeons and patients within your center. You also want to evaluate any financial implications and ensure that your facility is equipped with the necessary imaging technology and software to support the creation of custom implants.
While research on long-term performance and patient satisfaction of custom implants is currently limited, its growth doesn’t appear to be slowing any time soon. The future of custom implants lies in the development of personalized knee replacements that align with the unique kinematics of each patient, says Dr. Bostrom. As technology continues to advance and offers more options for customization, such as increased implant sizes and the integration of navigation and robotics, you can anticipate further progress in achieving optimal outcomes and patient satisfaction in joint replacement surgeries.
“I think as we understand kinematics and movement of the knee more, we’re going to be able to give patients a truly personalized knee replacement that fits their knee very specifically,” says Dr. Bostrom. “It’s a very long way away from that point, but maybe not as long as many people think.” OSM