Upgrading Fluid Waste Management Systems
By: Adam Taylor | Managing Editor
Published: 9/18/2024
Volume and services line largely determine which system is right for you.
The Shreveport (La.) Endoscopy Center found the type of fluid waste management system that’s right for them more than a decade ago and won’t be switching any time soon.
Outfitted efficiently
The seven-procedure-room facility is outfitted with a direct-to-drain system that pumps waste directly into the septic system. It’s a perfect solution for the scope center, which performs an average of 100 procedures each day, says the facility’s Endoscopy Operations Manager Cody Patterson. “We have dual-suction systems, which are stationary and installed on the wall of each room next to our sinks. Vacuum regulators pull the waste into two glass containers that are housed in a stainless-steel box on each wall. One tube connects to a scope and the other to anesthesia equipment,” says Mr. Patterson. “You suction off whatever you do during the case, and there’s a switch that you literally just turn off. When you do that, everything drains off straight into the wall and into the septic. Everything’s gone.”
The units paid for themselves long ago from saving on supplies and disposal fees that were part of getting rid of the waste without the units, most of which can be operated in a hands-free manner using a foot switch.
• A safer and greener option. Without the wall units, facility employees would need to use solidifiers and then place the waste in biohazard containers. The wall suctioning method is more efficient, less expensive and safer for staff because they’re not exposed to the waste at all, which could potentially include dangerous pathogens.
Preparing and transporting the waste to refuse containers, or pouring it into a hopper, always includes the risk of splashback of the fluids onto the staff. They could also be injured while lifting the heavy canisters and transporting them on wet floors that could lead to slips, trips and falls.
Upgrading to a modern fluid waste management setup is better for the environment as well. Practice Greenhealth, a group that works with healthcare organizations to reduce the amount of medical waste they produce, says modern closed systems significantly reduce the amount of waste generated in operating rooms.
• Installation, maintenance and repairs. Direct-to-drain units are easier to install in new-construction or remodeling projects, but they can certainly be retro-fitted into existing facilities, says Mr. Patterson.
When hiring the plumber after purchasing the unit, be sure they follow the specifications on the installation sheet from the manufacturer to the letter to ensure the system will drain and function optimally from Day One.
The glass containers in the box on the wall are not removable, so they must be cleaned in place. The manufacturer recommends which types of cleaning solutions that gets suctioned into the containers, soaked for a specified period of time and then flushed into the sewer.
From time to time, the solenoids in the system have to be removed and replaced to make sure the system continues to turn on and off as precisely as when it was new. The old ones can be sent out to be refurnished and reused, says Mr. Patterson.
• Mobile cart and wall-mounted systems. What option a facility picks essentially depends on the kinds of surgeries performed, the amount of fluid generated and the volume of patients who are treated.
“Everybody has a different workflow, so it mostly depends on that,” says Mr. Patterson. Mobile carts that have the suction canisters on them could be equally appropriate for a lower-volume scope center or a busy orthopedic ASC where procedures involve large amounts of saline and bodily fluids to dispose of. Facilities opting for the carts would need the space to store them and space to install docking stations to which the units connect to dispose of their contents and then be cleaned and flushed. “There is an approximately hour-long disinfection process before everything is emptied into a janitor sink drain, so it’s time consuming,” explains Mr. Patterson. “And the mobile units are significantly more expensive than the wall-suction systems. They’re certainly not a perfect fit for a high-volume endoscopy center.”
High-volume scope centers like ours that go with wall-suctioning units won’t be disappointed.
—Cody Patterson, Shreveport Endoscopy Center
But they may be a good option for an ASC with a total joints program, as they have canisters which may hold more fluid than the wall-suction unit at Mr. Patterson’s center. And facilities can trial the new products to see which is best for them.
(The company he uses does, however, have a larger wall-mounted direct-to-drain system designed for arthroscopy and other procedures that is billed as an alternative to cart and floor-flushing systems.)
When starting from scratch
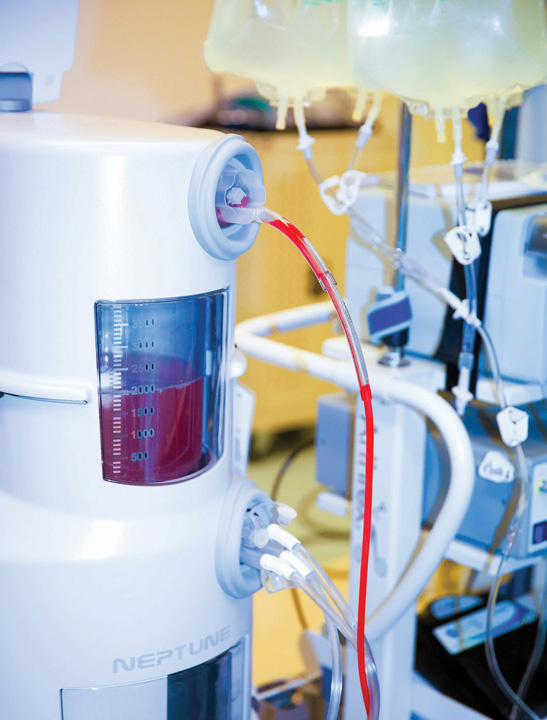
As Mr. Patterson notes, many surgical facilities are still disposing their fluid waste in old-fashioned ways. If you’re looking to make a change, the first step in the purchasing process is to assess your needs, he says.
“If I was a facility that is using old-school solidifier and containers, I’d start by analyzing my workflow,” he says. “I’d certainly trial a mobile cart system if I had procedures that generated high volumes of fluid and/or if procedures were conducted in different rooms all the time and I didn’t want to have wall units installed in every room, which becomes a price issue. But if I had dedicated rooms for dedicated procedures, or was operating with a lower patient load, I might just opt for a direct-to-drain wall option from the start.”
A center’s volume doesn’t only come into play when deciding which type of fluid waste system to buy. For example, if the choice has been made to opt for a mobile cart system, a lower-volume center could reasonably not choose the most expensive option, because the bells and whistles on the most expensive model might only be crucial for ASCs or HOPDs generating the highest volumes of caseloads.
Bring others in
Don’t limit the trial process to surgeons, as staff satisfaction with the new product will be key to its eventual success. Everyone in your facility should be involved, but make sure that all key considerations are taken into account. For example, leadership should be prepared to remind everyone that infection prevention should be a primary factor in a new product, not just its ease of use or suction power.
And, as always, investigate creative financing opportunities and service contract options. No matter which option is chosen, anything is better than manual dumping, says Mr. Patterson. “High-volume scope centers like ours that go with wall-suctioning units won’t be disappointed,” he says. “And the mobile carts are great too in facilities where they’re most appropriate.” OSM