Don’t Skimp on Surface Disinfection
By: Kimberly Jones, DNP, RN, CNOR, RHCNOC
Published: 5/16/2023
Standardize your cleaning techniques to improve staff efficiency without compromising patient safety.
The surgical services team at Ascension St. Vincent Mercy Hospital, a critical access hospital in Elwood, Ind., is proud of the exacting standards that we hold. However, one area that we improved upon after a Joint Commission survey a few years ago was our environmental cleaning services.
We are privileged to care for some extremely sick patients as well as perform general surgery, orthopedic, podiatry, ENT and urology cases in our two OR suites, and after being cited for cleaning deficiencies, I took control and helped turn things around.
Here are the steps I took to improve and standardize our surface disinfection protocols to help keep our facility clean and our patients safe.
Take control
It took a Joint Commission survey to realize our facility needed to clean up its surface disinfection deficits.
Like two other hospitals in the region, our facility outsources its environmental cleaning services, and all three of us ultimately needed to make changes. We learned that the EVS company we were using didn’t have the education and competencies to properly perform a terminal clean in our ORs. Even though the staff member who cleaned our ORs at the time had been there for 15 years, and did an absolutely remarkable job, I had to treat her as if she were a brand-new hire and start from the very beginning.
To develop a standardized surface disinfection process, I leaned on AORN’s evidence-based guidelines. I wanted to make sure every staff member on the environmental services (EVS) team knew exactly what was expected of them. For example, AORN recommends that you tackle items clean to dirty, top to bottom and clockwise or counterclockwise.
To make sure staff was following protocol, I’d stay and watch them clean once a quarter. I now only monitor the staff once a year, but I will always stay and observe whenever EVS hires someone new. In fact, a new staff member cannot clean by themselves until I have watched and cleared them. My team receives the same guidelines and training for cleaning, and I am routinely in the OR — often helping with turnover, so there are ongoing evaluations of the processes. Watching EVS and my own team clean can be a time-consuming process, but it’s worth it to know our surfaces are properly decontaminated.
When you are trying to turn things over quickly and you need to let a cleaning product sit for 10 minutes, you are wasting time and losing money.
Don’t dwell on it
There are numerous cleaning agents on the market, so it can be tough to narrow it down and pick the right products for your facility and procedures. One thing I always look at is the dwell time, or how long it takes for a cleaning agent to kill the organisms it is designed for.
When you are trying to turn things over quickly and you have to let something sit for 10 minutes, you are wasting time and losing money. The other piece to consider is how harsh the cleaning agent is on the equipment. For instance, bleach is great for killing C. diff, but it’s notoriously harsh on equipment. There are some chemicals that actually make plastic more brittle, making your equipment break down faster.
We use a combination of products, but we don’t use sprays, because we don’t ever want to question whether the chemical is being aerosolized or not. Instead, we use a lot of pour bottles. I have the choice of getting spray tops or pour bottle tops for the chemical that we primarily use, and we liked the pour top a whole lot better because it makes it much easier to saturate your surfaces. We also use pre-saturated wipes. For most of our surfaces, the product we use has a one-minute dwell time; however, we cannot use that same product on our surgical lights as it is not approved by the manufacturer of the lights. For our surgical lights, the approved product that we use has a three-minute dwell time.
With the pour bottles, we wipe down surfaces with a either a disposable rag or a low-linting cloth. Disposable cloths just make everything easier, but make sure that whatever you use is sturdy and is low-linting, because even a small piece of lint could get into a patient’s wound and cause a surgical site infection.
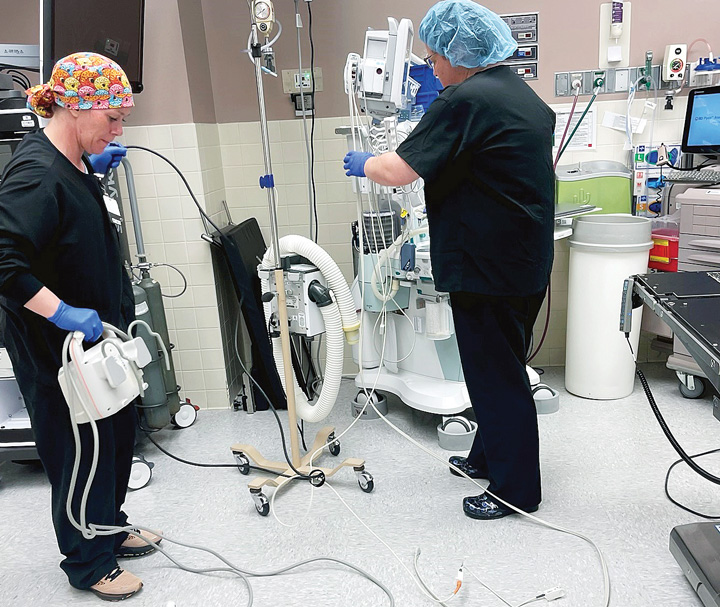
Turning over your OR can be a stressful time. You want to make sure you hit every surface, but you don’t want to throw the surgery schedule off track. “You should also try and keep clutter to a minimum,” says Kimberly Jones, DNP, RN, CNOR, RHCNOC, nurse manager of surgical services, oncology, audiology, wound care and medical specialty clinics at Ascension St. Vincent Mercy Hospital in Elwood, Ind. “If a space is overcrowded with clutter, there is a greater chance that your staff will miss a surface or piece of equipment and it will not get properly cleaned.”
To be on the safe side, keep a list of these high-touch objects (courtesy of AORN’s Guidelines for Environmental Cleaning) in the OR handy, so you can make sure you and your team tackle them before the next case.
- Anesthesia cart and equipment, such as an IV pole
- Anesthesia machine
- Patient monitors
- OR bed
- Reusable table strap
- OR bed attachments
- Positioning devices
- Patient transfer devices
- Overhead procedure lights
- Tables and Mayo stand, and
- Equipment, mobile or fixed.
—Danielle Bouchat-Friedman
Top-notch training

Unfortunately, there’s a lot of turnover in EVS, which means I’m often training new hires. The wonderful thing about my team is they are very engaged, and they take cleaning extremely personally. They want to do the right thing, and they also want to know when they aren’t doing something correctly. We actually receive a lot of compliments from our surgeons, because our turnover times are so much faster than our counterparts in the area. I think a lot of that has to do with planning and proper training. We are currently hovering around 20 minutes, which is much better than the national benchmark of 28.5 minutes; however, our team goal is 15 minutes, so we still have some work to do.
Don’t get discouraged
Sometimes it takes a slip up to get back on track. There’s no harm in taking a step back and looking at how you can improve your processes. I can proudly say that we’ve had three accreditation surveys since making these cleaning changes, and the Joint Commission has been extremely impressed with the cleanliness of our hospital with each visit. It may take a lot of hard work upfront, but in the end, keeping your patients safe, healthy and infection-free is always worth it. OSM
If you’re looking for a comprehensive listing of EPA-registered disinfectants, check out the handy tool on the EPA’s website. Visit osmag.net/productlist and click on the links under the heading: “Antimicrobial Products Registered with EPA for Claims Against Common Pathogens.”