The sterile processing department at my busy medical center was recently expanded to ensure instrument care could keep pace with the opening of new operating rooms and the addition of more cases. While the department’s new design elements and larger footprint have improved our overall workflow, rigid sterilization containers have been key in helping my staff keep the department running smoothly and efficiently. Here are some of the reasons why we rely on the containers to keep the department humming.
Appreciate the Benefits of Rigid Sterilization Containers
By: William DeLuca, CRCST, CHL, CIS I
Published: 5/24/2021
The systems are space-saving, sustainable and cost-saving solutions for busy sterile processing departments.
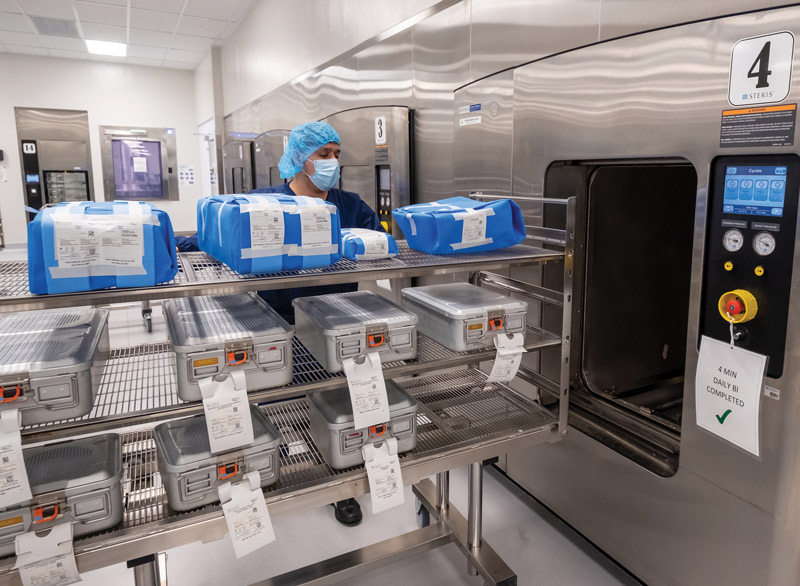
They save space and time
We reprocess around 400 instrument trays each day, and storage constraints are a constant concern. You can’t stack trays wrapped in blue wrap because of the risk of holes forming; stacking a tray that weighs 20 pounds on top of another tray with jagged edges and corners can tear open the wrap. Rigid containers are solid and stackable, so this isn’t a concern.
Rigid containers need to be sterilized between uses. We send ours through the case-cart washer, which might sound more time-consuming than the process of wrapping instruments in blue wrap. But remember, even the smallest tear in wrapped trays renders the instruments inside unsterile and unusable, meaning the set needs to be rewrapped and rerun through the sterilizer. This time-consuming task doesn’t come into play with impenetrable rigid containers. Plus, when you’re assembling instrument sets for sterilization, they can be placed in any appropriately sized container — you can grab one that’s available and get to work.
However, it’s worth noting that rigid containers might not work for all instrument trays. For instance, while wrapped trays and rigid containers tend to be similar in size, my hospital has numerous small and oversized trays that we must wrap because they don’t fit in currently available rigid containers.
They’re easy to handle
It’s easier to lift and transport a rigid container filled with 30 pounds of instruments than it is to move a tray of wrapped instruments that weighs the same amount. Wrapped instrument trays are various shapes and sizes, making it difficult to carry the packages. This can result in punctures and tears in the wrap that impede the productivity of instrument reprocessing. Rigid containers have two handles, one on each side, making them easier to carry.
The containers are also sturdy, so reprocessing techs don’t need to worry that the inevitable bumps and knocks that occur during transport and storage will contaminate or damage instruments.
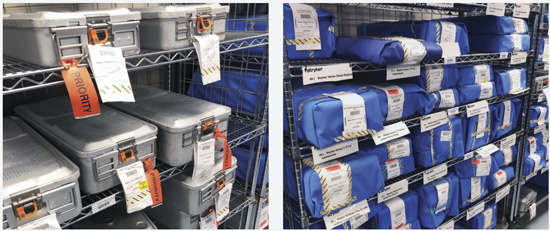
Here’s a breakdown of the annual costs associated with rigid containers vs. blue wrap. It’s interesting to see how they stack up and how from a purely financial perspective, rigid containers make the most sense.
— William DeLuca, CRCST, CHL, CIS
They’re eco-friendly
To appreciate the benefits of versatile rigid containers, first consider the different sizes, dimensions and weights of blue wrap that are available to meet the various needs of today’s central sterile departments. Most of our trays are wrapped with 48-inch x 48-inch wraps. This is because 20% of our inventory is on consignment, and the vendor trays fit perfectly within those wraps. The standard instrument tray is about 10 inches x 20 inches, and the 48-inch wrap is perfect for that size, too. It covers the tray fully, allowing its contents to remain sterile.
There are also different grades of wrap. The higher the grade, the heavier the tray you can wrap. The lower grade wraps, H100-H300, are mainly used for lightweight and low-profile items such as batteries, cords and small instruments. The heavier grade wraps, H400-H600, are meant for trays filled with more complex instrumentation. Before any tray is reprocessed, the instrument manufacturer’s IFUs must be reviewed. Some manufacturers require SPD to use a lightweight wrap because its thickness makes it difficult for the sterilant to come in contact with the instrument.
At my facility, we use wraps that are blue on one side and white on the other. To allow easier identification of our loaner trays, we wrap them with the white side facing outward. We have well over 2,000 trays in our inventory; imagine searching for a single loaner tray when they’re all wrapped in blue. With our method, white-wrapped trays stick out in the sea of blue wrap. The white and blue contrast also allows the surgical staff to identify pin holes in wraps after opening trays in ORs. When they hold the wrap up to the light, the contrasting colors make it easier to spot holes.
Blue wrap accounts for close to 20% of all operating room waste, according to Practice Greenhealth, which provides healthcare sustainability solutions. The material is recyclable, so train your staff to separate clean blue wrap from regulated medical waste, and make sure the collection and gathering process for recycling is easy to implement and follow.
The more you save by investing in rigid containers, the more money your facility will have to invest in higher-quality care.
The lifespan of reusable rigid containers is another major benefit that allows you to avoid the expense of working with blue wrap and manage the multi-step process involved in recycling it. Properly maintained containers should last at least seven years before they need to be replaced.
Smart savings
When it comes to the environmental benefits of rigid containers, they’re far superior to blue wrap. One aspect of containers that leaders balk at is the upfront costs of adding them to their inventory. A bit of number crunching suggests that concern is likely unfounded (see “Investing in Rigid Containers Pays Off”).
Remember, the bottom line is the bottom line. I see it like this: The more you save by investing in rigid containers, the more money your facility will have to invest in higher-quality care. Sometimes short-term or upfront costs are lower, but result in higher expenses over the long-term. We always look two, five and 10 years out when preparing for capital purchases or negotiating contracts with vendors to gauge the long-term benefits of the investment. If you have a limited budget, get creative and do your due diligence to find a deal that works for your facility. You should speak with the vendors you already do business with. They’ll sometimes offer an umbrella contract that involves multiple products at a discounted rate.
After performing a true cost comparison of rigid containers and blue wrap, and factoring in other benefits like storage, strength and the environmental impact, you’ll likely find that rigid containers best blue wrap in almost every way. OSM